FAQ
Any questions related to the application? Check if you can find the answers in our FAQ.
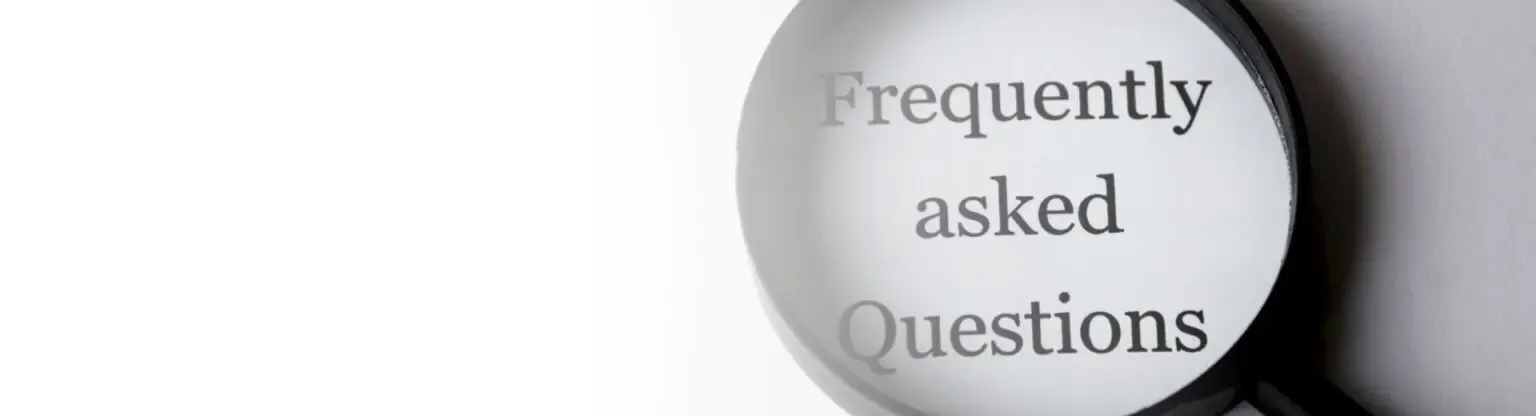
The recent years of industrial development have focused on spreading the quality management system based on ISO 9001 norm. It became a standard for an organization as well as for the customer to hold a certificate proving quality management. Looking at an organization as at a set of associated processes enabled to improve management efficiency and cost minimalization. Such an approach is used in each branch of present day economy, ranging from service companies, production companies up to administrative institutions.
The ISO 9001 norm introduces standards in all spheres of an organization functioning, paying special attention to issues connected with monitoring and measuring, following guidelines included in point 7.6 (Point 7.1.5 edition 2015). In spite of the fact that this point is relatively short, it gathers a great deal of significant information.
A natural consequence and at the same time development of the aforementioned point was the norm introduced in 2003 and marked as ISO 10012 – “Measurement management systems. Requirements for measurement processes and measuring equipment”. Another popular standard, defining requirements connected with measuring equipment for calibration and research laboratories is ISO/IEC 17025 norm – General requirements concerning the competences of research and calibration laboratories.
The summary presented below is a set of the most important requirements appearing in the norms mentioned above. To assure compliance with requirements, it is necessary at least to:
- Identify measuring equipment used to assure quality
- Keep a register of measuring equipment (carts, sheets, application)
- Set requirements concerning equipment (at least MPE in terms of the requirements of the measuring process)
- To set a calibration/ checking schedule
- Calibrate in predetermined time intervals, that is, comply with the aforementioned schedule
- Verify, adjust and repair, if necessary
- Keep records of the conducted activities
It is not an easy task to successfully manage a set of measuring equipment, frequently consisting of a few hundred (even a few thousand) devices, particularly in a situation when the calibration deadlines have to be strictly kept, and supervise their technical condition as well as current localization. Therefore, does an organization have to spend a great deal of financial resources as well as use a number of staff in order to maintain a full compliance with the system?
The answer is: NO - see the details below.
NEOGAGE enables managing measuring equipment in an unbelievably simple and efficient way. The most important elements of the software make it possible to get full independent from paper documentation. If you do not wish to give up paper documentation, you can easily attach scans or print reports and views directly from the application.
NEOGAGE METROLOGY revolutionizes management of measuring equipment – it is a tool which enables to monitor measuring equipment in a comfortable and efficient way in any company, regardless of the activity profile, management system or the type of the tools being used.
NEOGAGE ANALYSIS – contains a set of MSA analysis enabling verification and improvement of measurement systems as well as SPC module which enables statistical process control.
MSA Module contains three analyses:
- Cgk,
- GR&R,
- Attribute.
SPC Module enables the use of statistics and data to verify deviation from the required standards. Process stability analysis is carried out using four tools:
- histogram
- Pareto diagram,
- control card,
- process flow diagram.
NEOGAGE MACHINE CONTROL – enables registering machine cards in dedicated records, creating failure reports as well as converting them into internal orders or those carried out by an external contractor. The module also contains statistics on the timeliness of operations on machines and statistics showing the time of machine failure.
NEOGAGE TOOL MANAGEMENT – a module for tool inventory and management. It enables its users to track the equipment and record flow actions, such as an issue, return or exchange. In addition to this, Tool Management provides strong support in warehouse and stock management and allows to monitor the costs of tools thanks to the statistics feature.
NEOGAGE QUALITY CONTROL – a mobile application supporting the control of finished products by the quality department. It enables to keep records of tested products and carry out checks in accordance with the attached control cards that determine the correct performance of the action. Application users can be assigned specific roles and given specific permissions.
Full control
- Access to all kinds of data connected with measuring equipment from any place and device
- Checking the calibration status, the results and preview of the certificate directly on the production line or during an audit at the customer’s
- Automatic reminder of the checking dates
- Registration of a real user together with a dynamic update of the technical condition thanks to the rental module
- Complete information about the current state of the machine park
Saving time
- The application works instantly, no installation required
- Finding data takes seconds and takes place at any location in your company
- Labels with QR codes provide a preview of the data immediately after scanning with a smartphone or a reader
Compliance with norms requirements
- ISO 9001
- ISO 10012
- ISO 17025
- ISO/TS 16949
Reducing the risk and costs resulting from the lack of quality
- Monitoring of changes in metrological properties allows for early withdrawal of the tool
- Thanks to advanced reports , it is possible to identify critical points generating increased costs or downtimes (vendor, process, user).
- Reducing the risk of unavailability of key machines in the production process through complete information about failures and ongoing repairs and reviews
- Reduction of downtime thanks to immediate failure information generated by the automatic system notifications
The aim of the application’s developers is to create an effective tool for the management of company’s assets.
Implementing our system ensures that you minimise the risk of using inappropriate or faulty equipment and gain full control over your machinery and tools.
Quick access to data, centralised information, increased productivity and reduced costs associated with unplanned repairs are only a few of the benefits you get with NEOGAGE.
The overarching goal of our team is to develop a system that is sufficiently versatile and flexible, to make its adaption to company conditions and norms as easy as possible.
Another factor taken into account when developing the system was to maintain transparency and ensure convenient and simple use. In aim to meet prevailing trends of modern management, the system has been designed to be environmentally friendly - its functionalities minimise the need to use paper documents, which in turn results in increased work efficiency and time savings.
Asset Records
Dedicated cards of measuring equipment, machines, tools and other assets (such as company cars or health and safety clothing) allow you to collect all the necessary information in one place and quickly access your data by assigning each card a unique identification number.
Task Register
This is one of the most important functionalities in the application. You can monitor all scheduled maintenance activities and a list view with icons allows you to organise calibration or inspection in no time. Task register is a key element in maintaining compliance with the requirements of your system.
Access to Historical Data
The application provides you instant access to archived asset cards, historical records of performed maintenance activities, as well as instructions or attachments.
Asset Tracking
This functionality allows you to get full control over asset’s location, user or technical status. To make the process of checking-in and checking-out more automated,, we recommend the use of QR codes or RFID tags.
Location Structure
Create the list of locations where your equipment is used. Specify a city or town (if a company has several branches) and a department or production line. Assign assets to locations and identify them in the blink of an eye.
Employee Cards
The application enables you to create dedicated cards of employees who are also equipment users. As a result, you can compile a list of assets used by certain employees and quickly identify who is the user of a particular piece of equipment.
Documents
This section contains all documents created in the process of managing measuring equipment, tools and machinery - scans of certificates, maintenance and repair reports, etc. The feature is linked to asset cards and task records, allowing you to find and display a document with a few clicks.
Machine Failure Reporting and Work Order Processing
The system allows machine breakdowns to be reported and registered immediately. Employees responsible for supervising the machines receive an e-mail notification to keep response times as short as possible. The reported failures may be rejected or transformed into a work order. The NEOGAGE users can monitor the progress of the work order tasks and their lead time which guarantees full control over the entire process.
Automatic E-mail Reminders
With NEOGAGE, supervising maintenance schedule becomes much easier. The system sends automatic email notifications of upcoming or overdue activities on equipment as well as of documents that are about to expire.
Statistics and Reports
This functionality takes you to higher level of asset management. The application collects information on costs related to the purchase of equipment and maintenance activities performed on assets. In addition to this, NEOGAGE enables budget planning and monitoring the timeliness of work order completion. The users of the Machine Control module can monitor machine downtime thanks to the failure metrics.
Roles and Permissions
Create user roles with defined sets of rights and decide what level of access to data should be granted to a given employee - from limited preview of data to full system administration.
Audits will never be as they used to be.
NEOGAGE gives a possibility of checking data concerning a particular device from any place – enter the device number, display the history of checks and show an attached scan of the calibration certificate (it’s also possible on a mobile device).
Even in the basic version, the application has all modules necessary to supervise the measuring equipment in compliance with popular norms (ISO 9001 and ISO 10012). You can create transparent device cards, add employees and places of use. Thanks to legible lists and advanced filtering, you will inform employees or the department about the upcoming audits just with a few clicks.
The application focuses on simplicity and comfortable work. It is easy to imagine a situation, for example, when we can provide, e.g., an auditor with a valid calibration certificate directly on the production line. Another advantage is undoubtedly the lack of the necessity of installation and assigning to the position, which allows to reduce costs of additional license. Not without significance is the fact that a simple and transparent interface should assure comfortable work both for the younger as well as older users. With its whole simplicity, the application has got everything, which allows to maintain compliance with the requirements of the ISO 9001 norm – a full identification with the equipment and monitoring of the checks schedule.
NEOGAGE application is available in two models:
- NEOGAGE SUBSCRIPTION - an annual subscription together with service support (the subscription is connected with granting the customer the right to use NEOGAGE application for the period of 12 months).
- NEOGAGE LICENSE - a permanent licence + an annual service support (the permanent licence becomes the property of the customer, the customer can choose installation options on his own infrastructure or use the resources made available by UpWare Sp. z o.o. free of charge, provided the service support continuity is maintained).
Four versions are available for all NEOGAGE products, differing in functionality and the number of supported resources:
- Free
- Basic
- Standard
- Premium
For paid versions, additional expansion modules and packages are also offered. The comparison can be found in the LICENSING tab.
The service support (concerns the model of purchasing the permanent licence – NEOGAGE LICENSE) gives possibilities:
- To update NEOGAGE to the most recent version
- Reporting possible problems with NEOGAGE functioning.
- Receiving telephone advice for customers using NEOGAGE.
In case of purchasing NEOGAGE as a subscription model (NEOGAGE SUBSCRIPTION), the service support is included in the price of the subscription as a standard.
In case of using NEOGAGE in hosting, you only need a PC / Mac computer or tablet/smartphone with an Internet browser with an Internet access.
The NEOGAGE Quality Control application is available in the mobile version to download from Google Play and App Store.
In case of purchasing the permanent licence and installing NEOGAGE application on customer’s own infrastructure, a physical server or a virtual machine (Vmware, Hyper-V, KVM, Citrix XenServer) with a Linux Debian/Ubuntu/Redhat system – min. 2VCPU, 4GB RAM, 40GB HDD or Microsoft Windows Server 2019, or later (WSL support required) – min. 4 vCPU, 16GB RAM, 80GB HDD.
NEOGAGE uses MSSQL Database Server 2019 Express or higher. The server configuration depends on a number of parameters, among others, on the number of users, the number of devices in the database, the number of actions, etc. NEOGAGE engineers make the choice of the suitable configuration on the basis of data received from the customer.
For security reasons, backups should be made of the NEOGAGE application in accordance to the customer’s backup policy.
NEOGAGE application which is available in the cloud has got a number of advantages, such as:
- Time of making the application available to client and shortening of the implementation time (virtually “straight away”)
- Convenience of use and no maintenance
- Data security (everyday backup, firewall protection, anti DDoS)
- Lowering costs of maintaining the application with respect to the local solution on own infrastructure
- Always the latest version of the application
- Efficiency guarantee
- Monitoring of the application availability and efficiency
NEOGAGE uses a range of mechanisms protecting the customers’ data both stored in the database as well as transmitted via the Internet network by means of
- Encrypting transmission between the customer’s browser and the application using the SSL protocol
- Everyday backup of data with the replication to the backup center
- A continuous monitoring of servers performance and application availability (SLA)
- Protecting against DDoS attacks
- Using a fully scaled and redundant IT infrastructure
Yes, the export option is available in terms of all entered objects and generated data, such as: device cards, places, employees, documents, actions, rentals, statistics and reports.
Available formats of the exported data: HTML, CSV, TEXT, Excel, PDF.
Yes, there is an option to transfer NEOGAGE both from hosting to the client’s own infrastructure or from the client’s server to hosting.
Available formats of the exported data: HTML, CSV, TEXT, Excel, PDF.